Image credit: MIT
MIT researchers developed a new technique to fabricate electronics into textiles and claimed that those smart textiles have properties like flexible, washable, durable, and also comfortable.
The rapid advancement of electronic devices and fabrication technologies have been developed in recent decades. This advancement has certainly further promoted the field of wearables and smart textiles but seems not enough to create a wearable smart textile that exhibits the properties the same as nonsmart textiles. One important area that will be served by smart textile in the coming days will be the health sector. Researchers imagine using a smart textile in tracking health activity like precisely detect various physiological signals from the human body, such as electrophysiology, temperature, pulse oximetry, blood pressure, hydration, and others. For this, we need to integrate electronics into textiles and thus produced textile must be washable, can be exposed to dirt and humidity, intact to the robustness like friction and multiple stretching, etc. But developing smart textile with properties like washable, and intact to the robustness like friction and multiple stretching is a hard task with the now available concepts and design.
Several efforts, to fabricate electronics on the textiles, like coating textiles thread with metal or printing conductive inks on fabrics to serve as electrodes for electrophysiology, sewing and attaching functional threads and fabrics, weaving electronics fabricated on polyimide strips for humidity, temperature, pulse oximetry (measuring the proportion of oxygenated hemoglobin in the blood), and gas sensing many more have already been developed but these intelligent textiles are not scalable for large-area sensing and do not allow stretchability for the application of skin-contact sensing for electronic suits and we need more advanced smart textiles.
Canan Dagdeviren, the LG Electronics Career Development Assistant Professor of Media Arts and Sciences at Massachusetts Institute of Technology (MIT) said, "We can have any commercially available electronic parts or custom lab-made electronics embedded within the textiles that we wear every day, creating conformable garments. These are customizable, so we can make garments for anyone who needs to have some physical data from their body like temperature, respiration rate, and so forth."
Now MIT researchers have developed a technique that can combine thin, customizable conformable electronic devices, including interconnect lines and off-the-shelf integrated circuits, with plastic substrates that can be woven into knitted textiles using an accessible and high-throughput manufacturing approach. Their design allowed them to create shirts or other garments that could be used to monitor vital signs such as temperature, respiration, and heart rate.
A paper describing the work was published in the journal npj Flexible Electronics on 23 April 2020.
The team demonstrated their newly designed electronic textile conformable suit (E-TeCS) can have wireless physiological sensings, such as temperature, respiration, and heart-rate detection, and physical activity monitoring around the human body during a physical exercise.
They claimed that their technique creates a platform to integrate a large combination of conformable electronic components in a suit and also they are capable of sensing physiological and physical activity on the body.
The team tailored the electronic textile conformable suit from a customized fabric that can be integrated with an assortment of sensor integrated circuits (ICs) and interconnects in the form of flexible-stretchable electronic strips. The textile mainly consisted of channels or pockets for the weaving of these electronic strips. The sensor ICs and interconnects were developed by using two-layer industrial flexible printed circuit board (PCB) processes with required additional steps for chip and passive component assembly.
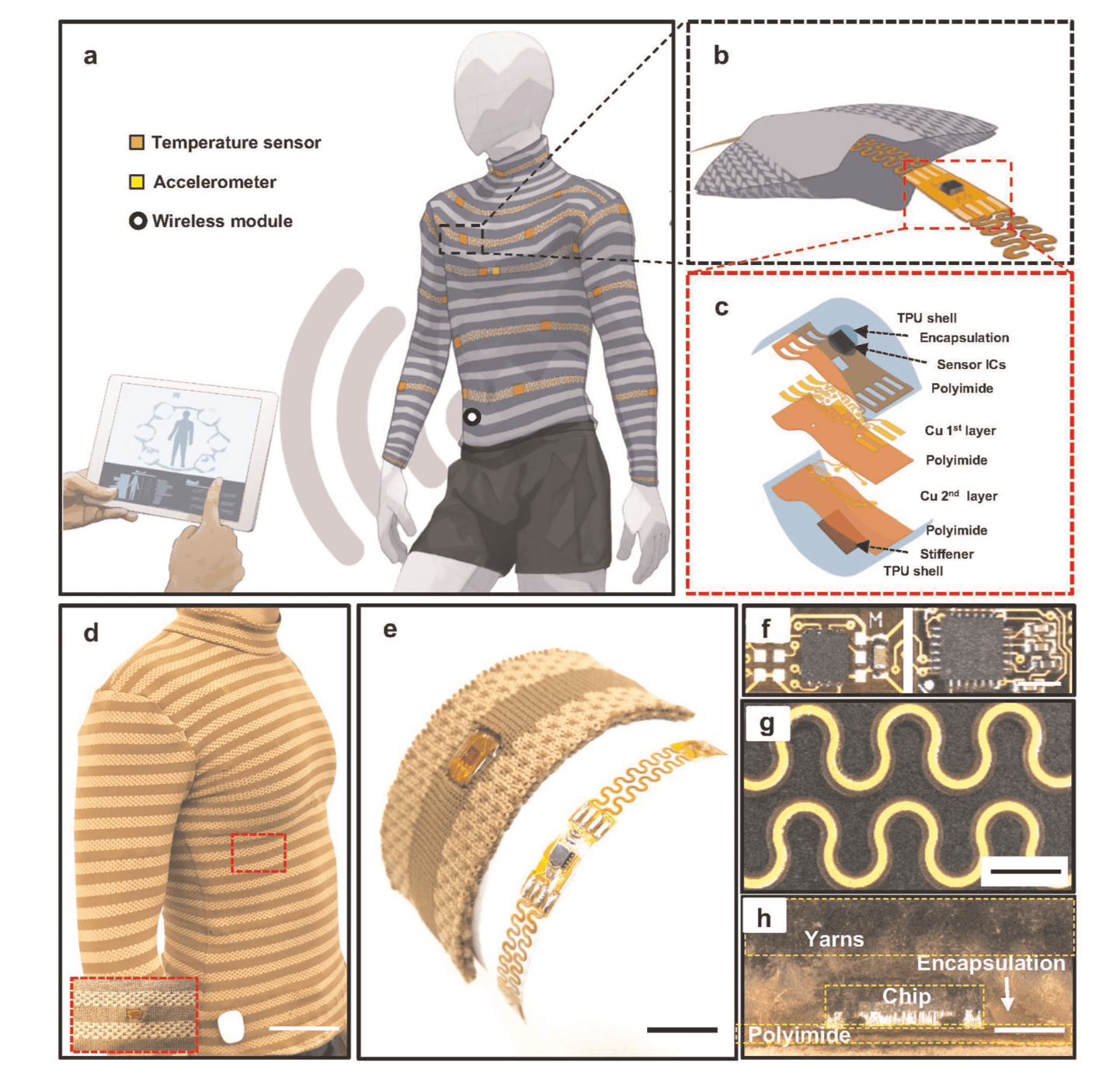
The sensor module of (e) (of above figure) consisted of two-layer flexible PCB and also Cu traces and polyimide. The MAX3025 (Maxim Integrated) sensor IC was soldered with a Pl stiffener as a support structure and encapsulated with 150 μm thick washable encapsulant (PE773, Dupont). The whole module was then encapsulated in a TPU shell with 100 μm thickness for each top and bottom layer. For the imaging purpose, they submerged and cured an electronic device woven into a fabric channel in a Polydimethylsiloxane mix with base and curing agent ratio of 1:10 bath. By this process, they designed and fabricated seven different modules: four temperature sensing modules, one inertial sensing module, and two interconnection modules.
Now the team developed knit fabrics by a digital flat two-bed knitting machine. With a two-bed knitting machine, single layer fabric can be realized by interlocking. Two yarn carriers were used in order to make two layers of weft-knit fabric. Weft knitting is a method of forming a fabric in which the loops are made in a horizontal way from a single yarn.
For the interlocking, they used two sets of needles that knit back-to-back in an alternate sequence to create two sides of the fabric that are exactly in line with each other, forming one layer.
Textile channels for electronic integration were knitted by allowing both the front and back needle beds to knit simultaneously and by making a spacer fabric with a hollow channel and the rest of the fabric was formed through interlocking.
Then the knitted fabric was laser-cut with the open channels positioned in a horizontal orientation. Now the sensor electronics were enclosed by using medical and semiconductor grade epoxy resin that is machine washable for both mechanical and electrical protection and the electronic strips were then further encapsulated in a stretchable outer shell.
Every sensor is exposed through the opening and glued to the textile with washable fabric glue (OK to Wash-It, Aleene). Four power and signal wires from the main hub were threaded to every end of these strips to connect the microprocessor to all available sensors.
For the temperature characterization, they embedded a temperature sensor in a piece of fabric and encapsulated by a thermally conductive epoxy and thermoplastic polyurethane. Then the electrically packaged sensor was placed on the surface of a hot plate with direct contact and the sensor was heated from 25 °C to 50 °C on the hot plate at a ramp rate of 300 °C/h. A high accuracy IR camera that was fitted into the sensor record the data when the temperature on the anodized Aluminum plate ramped up. Also, a micro-controller (Arduino UNO) simultaneously gathered data from all three flexible temperature sensors and logged these sensor data to a computer. The fitted IR camera has a thermal sensitivity of 40 mK.
The researchers designed a prototype shirt with 30 temperature sensors and an accelerometer that can measure the wearer’s movement, heart rate, and breathing rate and tested successfully that the garment can then transmit this data wirelessly to a smartphone.
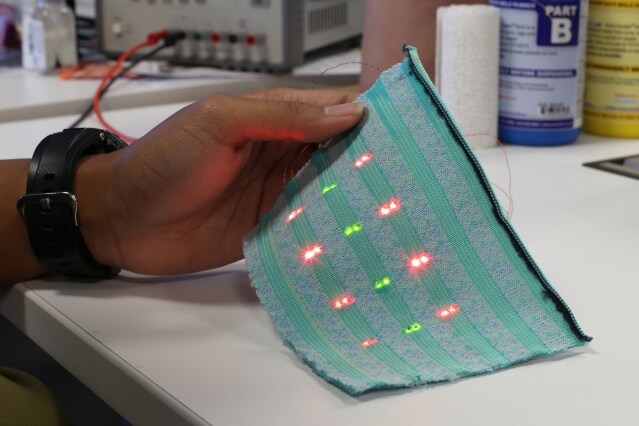
During the whole process, researchers used a polyester blend fabric due to the properties of polyester such as its moisture-wicking properties and its ability to conform to the skin.
Dagdeviren said, "From the outside, it looks like a normal T-shirt, but from the inside, you can see the electronic parts which are touching your skin." Dagdeviren added, "It compresses on your body, and the active parts of the sensors are exposed to the skin."
This new sensor-embedded garments, which are also machine washable, can be customized to fit close to the body of the person wearing them. Also, this type of sensing could be useful for monitoring people who are ill, either at home or in the hospital, as well as athletes or astronauts.
Dagdeviren said, "You don’t need to go to the doctor or do a video call. Through this kind of data collection, I think doctors can make better assessments and help their patients in a better way."