Image Credit: Caltech.
There is no doubt that the development and engineering of materials could lead us to the next phase of evolution. They could have direct consequences on the crucial field of space exploration to the omnipresent materials. Scientists at Caltech in collaboration with JPL, zeal to explore material engineering, have developed a material inspired by chain mail that can transform from a foldable, fluid-like state into specific solid shapes under pressure.
Structured fabrics, such as woven sheets or chain mail armors, derive their peculiar properties both from the constitutive materials and their geometry by which we can design their desirable characteristics, such as high impact resistance, thermal regulation, or electrical conductivity. These make them a field of high interest for the researcher. And obviously, the fabrics’ properties are usually fixed and limited.
The team demonstrated structured fabrics with tunable bending modulus, consisting of three-dimensional particles arranged into layered chain mails. The basics idea is, the chain mails conform to complex shapes, but when pressure is exerted at their boundaries, the particles interlock, and the chain mails jam.
The team was inspired by ancient chain mail armor and topologically interlocked elements.
Smart fabrics are wearable materials that sense and respond to environmental stimuli, varying their properties and/or measuring and communicating data to external recording devices and also include medical monitoring, wearable computing, and energy harvesting. Most of the fabrications in existence deal with integrating ‘smart’ components, such as flexible electronic circuits for sensing and computing, phase-changing materials for thermal regulation, or photovoltaic materials for solar energy harvesting giving focus on sensing and data communication.
Fabrics with adaptable or tunable mechanical properties could provide mechanical feedback to human bodies and perform functions such as joint assistance, support, and haptic perception and so the team introduced a type of architected fabric, consisting of chain mail layers with designed particles, that can reversibly and gradually switch between soft and rigid states. They write ‘such a fabric, with its tunable mechanical properties, is a promising candidate for smart wearable applications’.
Chiara Daraio, Caltech's G. Bradford Jones Professor of Mechanical Engineering and Applied Physics and corresponding author of a study says, "We wanted to make materials that can change stiffness on command”. Daraio added, “We'd like to create a fabric that goes from soft and foldable to rigid and load-bearing in a controllable way." An example from popular culture would be Batman's cape from the 2005 movie Batman Begins, which is generally flexible but can be made rigid at will when the Caped Crusader needs it as a gliding surface”.
The basic building blocks of this team’s designed fabrics are discrete, granular particles. There exists a change in mechanical properties of assemblies of granular particles and structure during jamming. Jamming is a phase transition that does not rely on temperature changes, as in ordinary materials but is instead controlled by local geometric constraints in granular matter.
Fabrication and Characteristics:
The structured fabric consisting of two layers of interlocked granular particles and each particle is a hollow, three-dimensional (3D) structure, constructed from connecting trusses, designed to reduce the overall density and enhance contacts between elements. The team chose octahedral particles because their 90° rotational symmetry enables the formation of a square 2D lattice in the interlocked configuration, and their sharp corners increase contacts between layers.
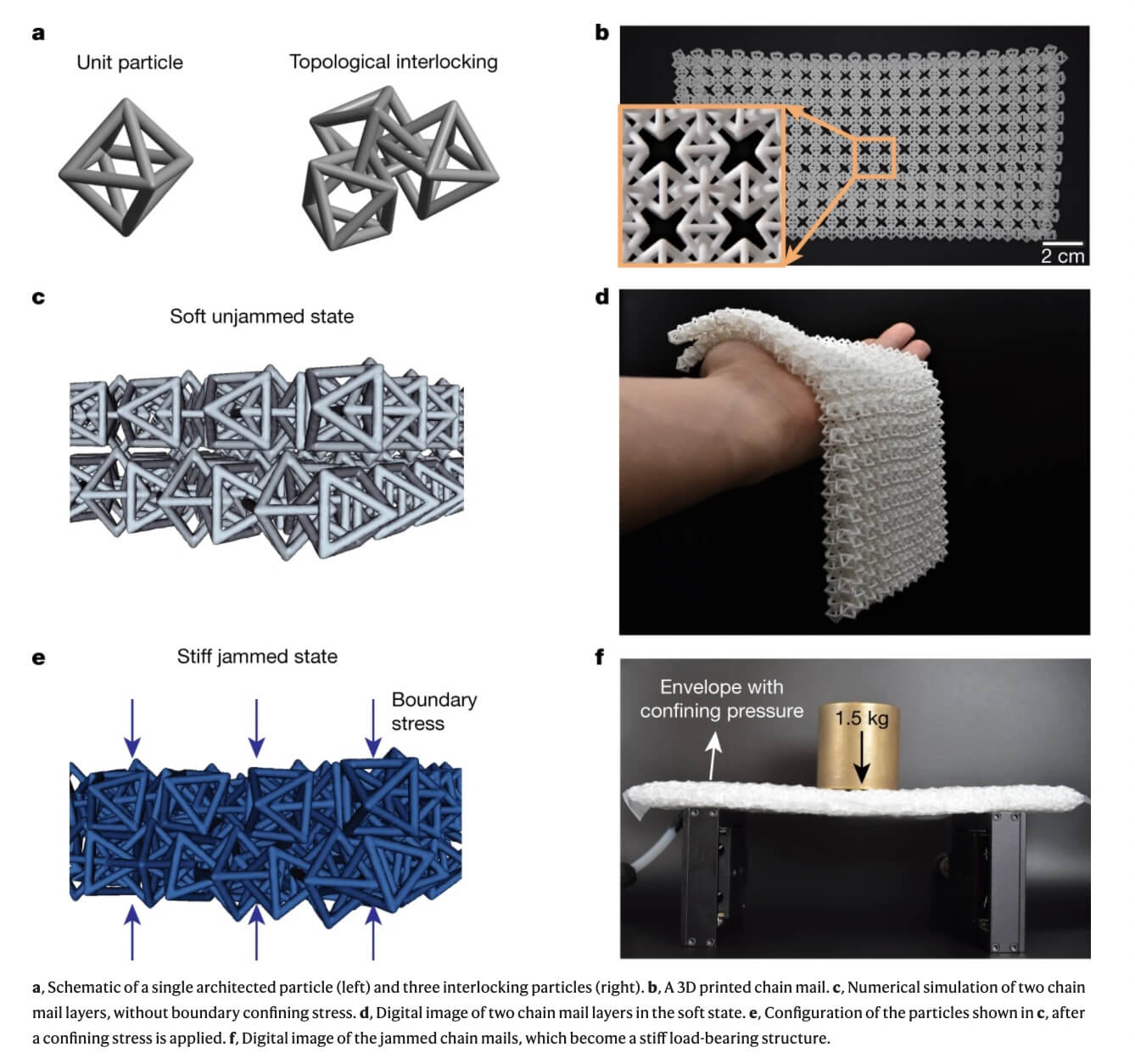
Now, they created the chain mail created by rotating neighboring particles 90° with respect to each other and by topologically interlocking all particles without forming solid connections where the interlocked lattice was manufactured using a selective laser sintering method, which prints the lattice in one piece without extra supports. They stack two chain mail layers to increase the number of contacts. What they found is like chain mail armor, the resulting structured sheets can freely bend, fold and drape over curved objects.
The team avoided the physical link between layers so to allow sliding between layers and result in higher flexibility.
Seeking to trigger jamming between the interlocked particles, the team applied variable compression at the boundary. By doing so, they also tried to tune the effective mechanical properties of the fabric.
The team enclosed the two layers in an airtight, flexible envelope, where the layers are weakly coupled and can still bend easily. To induce jamming, they apply a confining gauge pressure (pumping air out of the envelope), which causes confinement stress at the fabrics’ boundaries. This increases the particles’ overall packing fraction, triggering a jamming transition that increases the bending modulus and turns the fabrics into load-bearing structures.
To quantify the change in mechanical properties as a function of increasing confining pressure, researcher supports the sample at two edges and a line-shaped indenter is applied to the center of the top layer. They applied outside stress, compressing the fabrics using a vacuum chamber or by dropping weight to control the jamming of the material. They measured force−displacement curves which showed an initially linear regime, at small indentation depths, governed by the elastic behavior of the jammed granular structure.
They see that a vacuum-locked chain mail fabric was able to support a load of 1.5 kilograms, more than 50 times the fabrics' own weight.
As indentation increases, a nonlinear response is observed, probably due to frictional sliding and local rearrangement of the particles. This visually confirmed that the sample is adjusting its flexibility depending on the pressure we imposed on it.
Materials that change properties in similar ways already exist all around us, Daraio notes. "Think about coffee in a vacuum-sealed bag. When still packed, it is solid, via a process we call 'jamming.' But as soon as you open the package, the coffee grounds are no longer jammed against each other and you can pour them as though they were a fluid," she says.
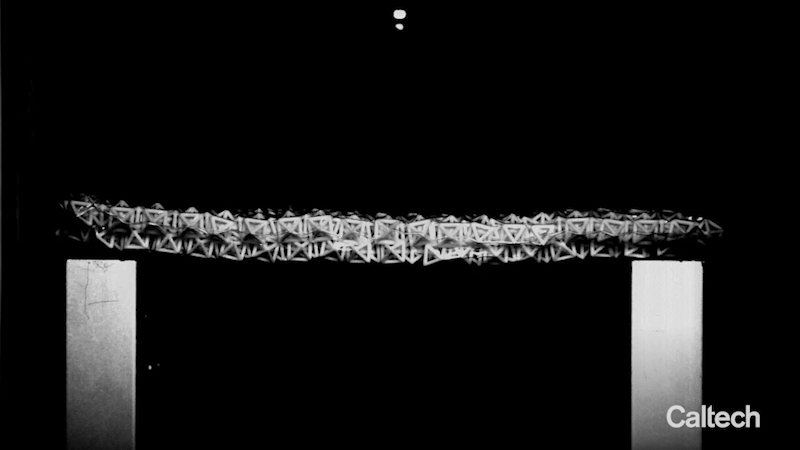
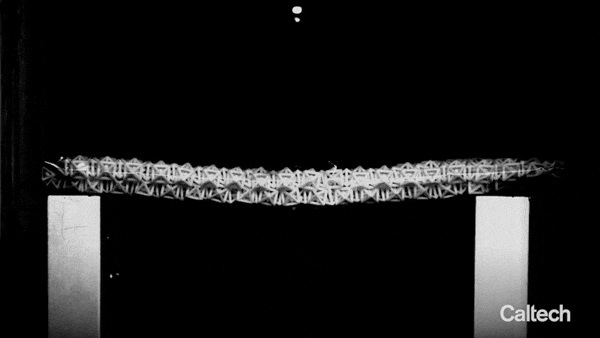
In parallel work on so-called smart surfaces, which are surfaces can change shapes to specific configurations at will, Daraio, together with postdoctoral scholar Ke Liu and visiting student Felix Hacker, recently demonstrated a method for controlling the shape of a surface by embedding networks of heat-responsive liquid crystal elastomers (LCEs), thin strips of polymer that shrink when heated. These LCEs contain stretchable heating coils that can be charged with electrical current, which heats them up and causes them to contract. As the LCEs contracted, they tugged at the flexible material into which they were embedded and compressed it into a predesigned solid shape.
An assistant professor at Nanyang Technological University in Singapore, Yifan Wang said, “These fabrics have potential applications in smart wearable equipment: when unjammed, they are lightweight, compliant, and comfortable to wear; after the jamming transition, they become a supportive and protective layer on the wearer's body”.